The rich and sumptuous variety of Rajasthan’s textile traditions and their ornamentation offer some of the most vivid pictures of its cultural moorings. Driven by versatile and sustainable eco-friendly techniques this heritage is a fabulous celebration of traditional forms of art, be it the organic, back–to–nature hand block printing or the mystery of bandhej—all driven by the sun, wind, earth and water in the masterly hands of its chippa. It’s a celebration of the immense variety of its ornamentation heritage...be it the embroideries in cotton and silk, in silver and gold or the intricate applique work. Now more than ever is it imperative that these treasured crafts be praised and preserved for posterity, not just as fossilized items in museums but as an inextricable eco-friendly part of everyday life. Here are 8 textiles from Rajasthan that you should know about:
Bandhej
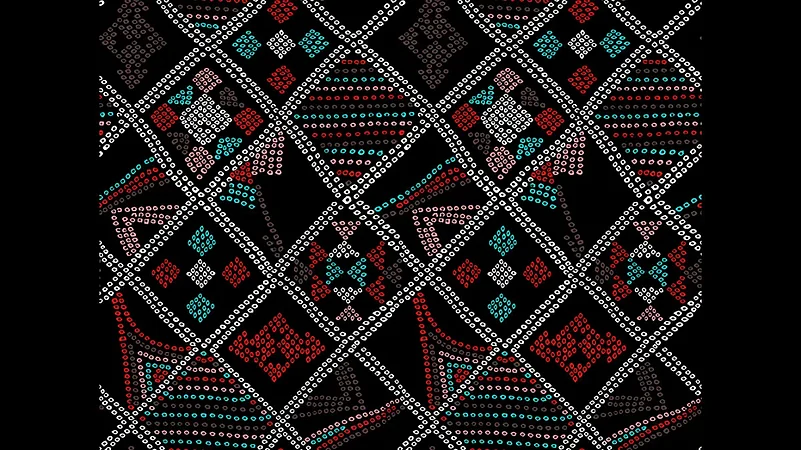
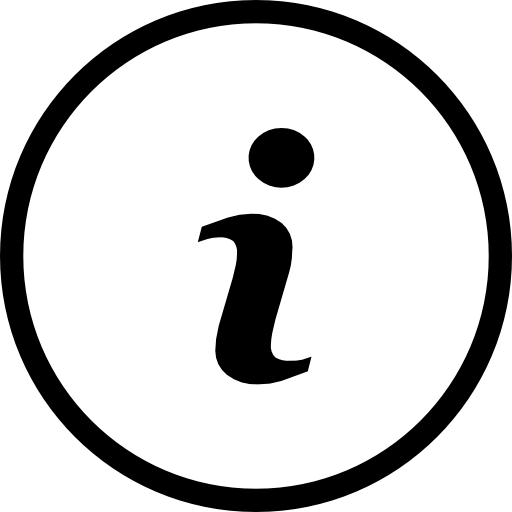
This iconic textile, also known as bandhini or tie-and-dye work is rooted in Rajasthan’s ancient handcrafted Maru-Gurjar tradition. Though there are indications from some references that the craft found its way into Rajasthan in the form of lehariya (the much beloved wave-like print), the common belief, however, is that it entered Gujarat’s Kutchi textile traditions from neighbouring Sindh with the Muslim Khatris, who are still largely linked to the craft. Jaipur, Jodhpur, Udaipur, Nathdwara and Sikar are known to produce the best bandhej work. Involving a very complex technique, bandhej undergoes multiple processes to achieve those beautiful outcomes in the different styles that have become so popular; chief amongst these are the ekdali, mothda, shikari and lehariya. The most prominent designs in bandhej are Dungar Shahi (hill shaped), Khat ka Laharia (single wave stripe), Laddoo-Jalebi Pomcha (yellow chunari), Chaubasi (groups of four), Tikunthi (circles and squares in groups of three), Satbandi (groups of seven), Ekdali (one dot), Boond (small dot with a dark centre) and Kodi (teardrop). The basic process calls for fabric (it could be handwoven cotton or silk) on which the design to be dyed is imprinted (rekhi) or outlined (with fugitive colours with either wooden or iron blocks. The marked dots of the design on the fabric are then tied with dye-resistant thread; to get rid of the design imprint, the cloth is given a thorough wash before it is dipped in the dye, rinsed, dried and then dipped in dye again. The leading colours used are yellow, red, green and black. Originally only organic mineral dyes were used for bandhej. The colour gold is used for overprinting or what is known as khan work.
Sanganer Hand Block Prints
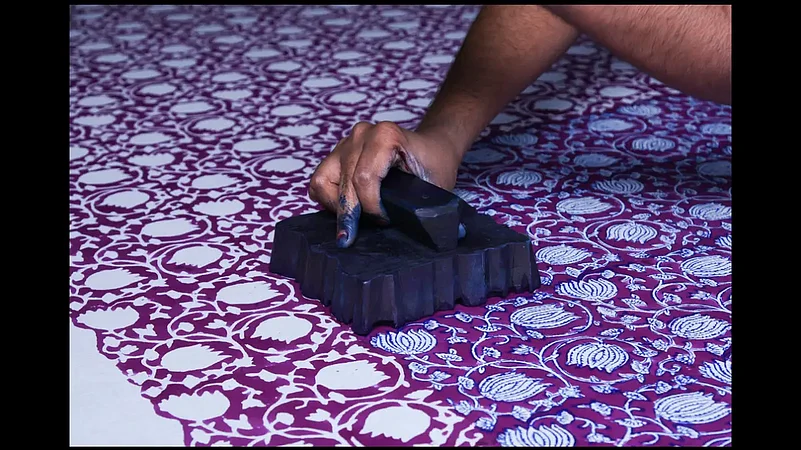
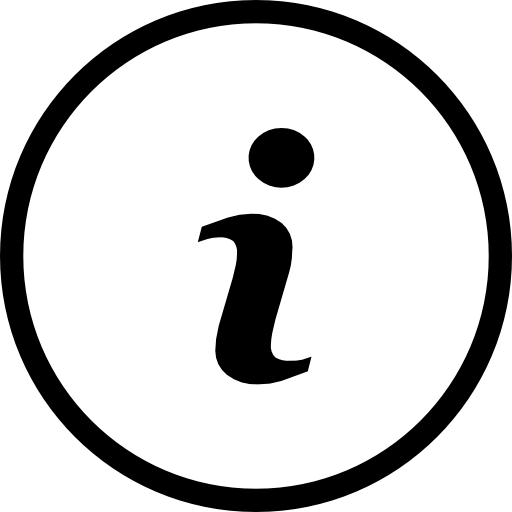
Much loved for those tiny decorative and delicate floral patterns or ‘boota-booties’ translated on fine cotton, muslin and silk the town of Sanganer’s hand block print work is an intrinsic part of Rajasthan’s textile printing narrative. With its revival back in the late 1960s, after going into decline in the 50s, Sanganer’s Calico prints (marked by their dual colour prints done repeatedly in diagonal rows) and Doo Rookhi prints (set on both side of the fabric) were transformed by their modern avatar as fashionable clothing for a growing export market. Sanganeri prints can be found on running cloth, sarees, dupatta’s, salawar-kameez sets, skirts, scarves, dresses, soft furnishings such as curtains and light-as feather quilts and dohar blankets. In the early days Sanganer’s finest block-printed fabric was only patronised by the royals and rich merchants. Sanganeri hand block print (chintz) which entered the European market through the East India Company, and was much trea- sured for the original organic mineral dyes used for printing designs. Today, available in mulmul or cotton voile, cambric and sheeting fabric by the yard, this historic textile town beautiful home craft serves a huge domestic and export market. Hailing originally from the Punjab and the Sindh regions the dyers and printers, who settled here, are from the traditional chhipa community. The wooden blocks (bunta) used by them for printing are found in different shapes and sizes. The water from the Sanjaria River (that once ran through the land) used in the printing pro- cess had a very unique property which gave the natural dyed fabric a particular radiance. The river water used in preparing Sanganer prints resulted in darker tones on the cloth whereas the water on Bagru prints brought out a reddish tone. Unlike the block prints of Bagru village, Sanganeri block prints are done on a white or off-white base; Bagru prints favour a red-and-black background. Common floral motifs in Sanganeri prints are roses, lotuses, sunflowers, lilies, marigolds, rosettes and lotus buds.
Bagru Hand Block Prints
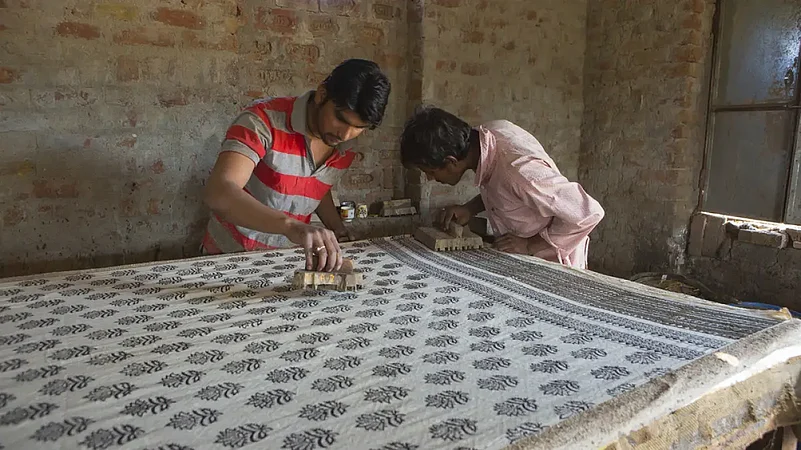
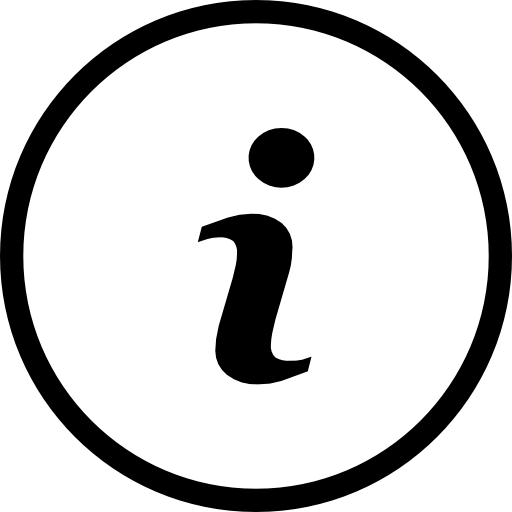
The over four hundred years of block-printing history of Bagru village has formed an important chapter in the textile legacy of Rajasthan. The chhipas of Bagru who settled here originally hailed from Sawai Madhopur, Alwar, Jhunjhunu and Sikar districts. It is no coincidence that the block-printing narratives of both Bagru and Sanganer villages reflect their humble origins and eventual rise to thriving expansion in both the domestic and export markets. Bagru is famed for two forms of block printing traditions—direct dye (typically indigo) printing and mud-resist dye printing, reflected in the Seyahi-Bagru and Dabu prints respectively. Direct printing entails the fabric being bleached first, then dyed and finally printed using the hand block by the chippa. Bagru prints are characterised by circular designs, as well as linear and floral patterns; the motifs, inspired by the floral, vegetative and faunal world, show Persian influences brought in by the Mughals which resulted in more geometrical patterns. Bagru motifs set in bold lines tend to be bigger than the Sanganeri motifs which are finer and more detailed. Patterns were formed in hues of indigo blue, alizarin and vibrant yellow on coarse cotton cloth by the indigenous processed of dyeing and printing. Bagru prints are done on off-white, ivory white or beige background. The main print- ing comes in black, red and maroon. Though the made-ups may have moved up from bedspreads and quilts to kaftans and midis to attract the new clientele, there is a continuity still, in the basic techniques and colours in Bagru prints from the olden days.
Lehariya
A popular print found commonly adorning phaganya odhni in the springtime during the festival of Holi, lehariya is a zigzag pattern replicating waves created by multiple mud- resistant and dyeing processes. Translated on thin cotton, fine silk, chiffon or georgette, it finds its natural oeuvre in the form of dupattas, turbans and sarees. As recorded by World Textiles: A Visual Guide to Traditional Techniques, the fabric is “rolled diagonally from one corner to the opposite selvedge, and then tied at the required intervals and dyed”. Go for the one worked in natural dyes, multiple washes and indigo or alizarin in the last stages of its creation. Marwari merchants and local traders in the 19th and early 20th centuries favoured the vibrant lehariya patterned fabric for their turbans, especially for special occasions and certain seasons. There’s pachrang in yellow, red, green and blue; the samudra lehar in the colours of the sea and the indradhanush, in the seven colours of the rainbow worn in the rainy season. Sombre occasions demanded more sober hues such as mauve and brown, detailed in tiny mothara. The cities of Jodhpur and Jaipur are renowned for their lehariya work.
Mothara
Set along the lines of the lehariya-making process, mothara requires an additional step in dyeing. The original resists are removed and the fabric is re-rolled and tied along the opposite diagonal, resulting in the iconic checkered pattern, marked by the small mothara (lentil-sized) spaces which are free of the dye.
Ajraks
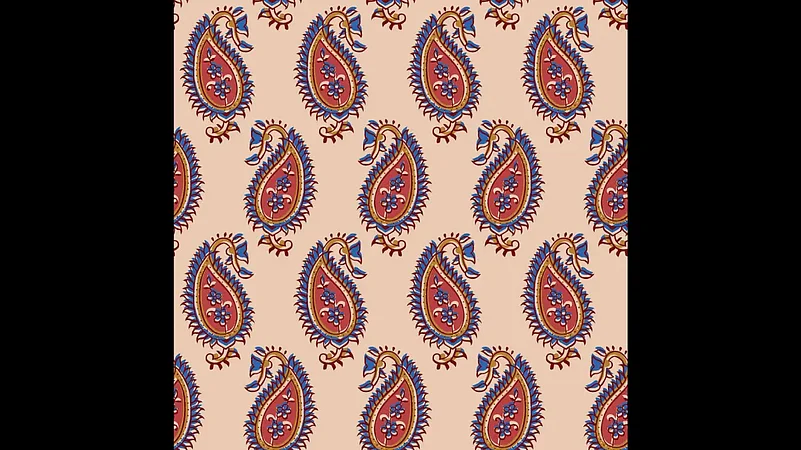
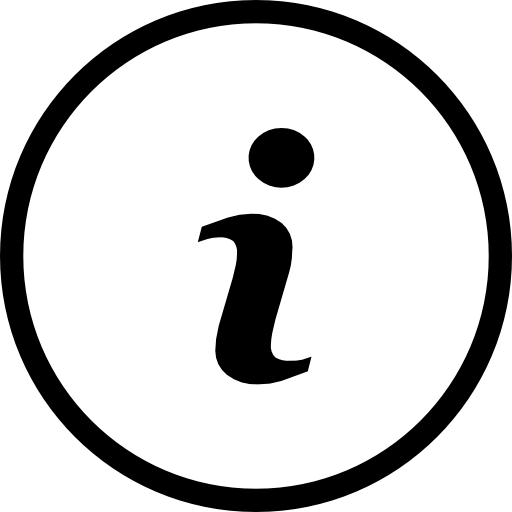
Geometric-themed patterns, printed on both sides of the cotton fabric by a method called resist printing, are best reflected in Barmer’s red and indigo ajraks. Again the printing process undergoes various steps including scouring, mordanting, printing, lime-resist printing, multiple dyeing in natural dyes of indigo (the key dye) and majistha (red) and washing. Printing is done by hand with handcarved wooden blocks. Barmer prints are principally featured in soft furnishing. Bedspread and bedsheets sell like hotcakes both at home and on the export market.
Jajam Textiles
The cultural significance of the Jajam as one of Rajasthan’s most important heritage crafts should not be underated. Traditionally created by artisans from the Chittorgarh region the unique craft of Jajam textiles, a block- printed floor covering coloured in traditional shades of red and black, is facing extinction; the best place for visitors to look upon such work is the Anokhi Musuem in Jaipur. The large patterned Jajam textile evolved out of a social tradition of village life and is often referred to as’ the people’s textile’, as it served as a thin floor covering for the community to congregate at a courtyard, temple or house — or any social occasion, religious ceremonies or festivities. It could also be a gift for the bride. At the heart of it, the diamond-patterned cloth would feature a game-board setting for playing chaupad, the Indian-style chess game. Its borders would often feature warriors, tigers, elephants and scorpions, symbols of protection from danger.
Kota Doria
This exquisite, light-as-gossamer woven fabric is perfectly scripted from Rajasthan’s hot cli- mate. This transparent weave, with its iconic square checks (khat) pattern is traditionally done on a pit loom by women in their homes in the villages of Kaithoon, Siswali and Mangroal. An indigenous solution of onion juice and rice paste is smeared on the fabric to strengthen it.