We mark the anniversaries of people, even institutions, but seldom keep track of the age of the magnificent structures surrounding us, till one day, they begin to show signs of distress, and a witch-hunt begins to identify a scapegoat! It was, therefore, a surprise when that warm invitation came from the engineering advisor to the Prime Minister of Bangladesh. It was the centenary of the famed Hardinge Bridge (aka Sarah Bridge), across the lower Ganges. My association: I was the engineer entrusted with repair of major damages inflicted on it during the 1971 war. An unusual assignment, it had called for innovative solutions, and urgently—the railway bridge was the lifeline of a newborn country recovering from war. Now, we got a fabulous reception, including a trip to the bridge by a special train. Judged against the utter negligence the engineering community suffers in our country, being honoured thus was a dream come true.
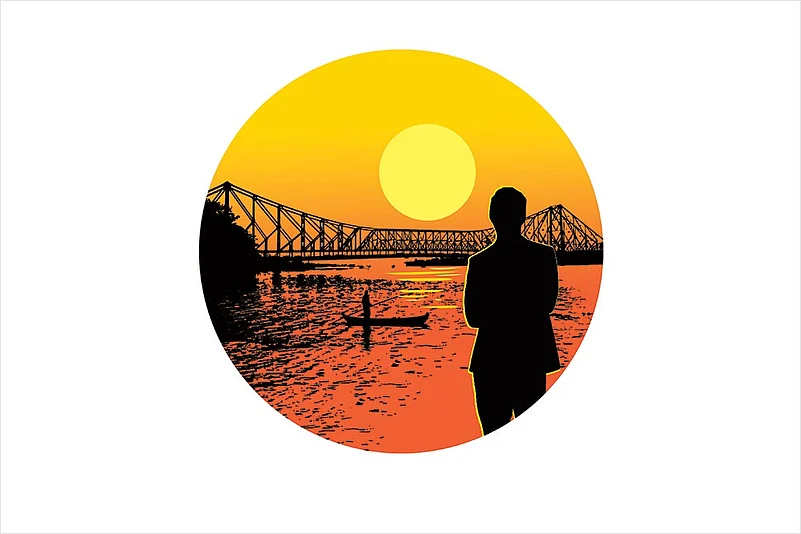
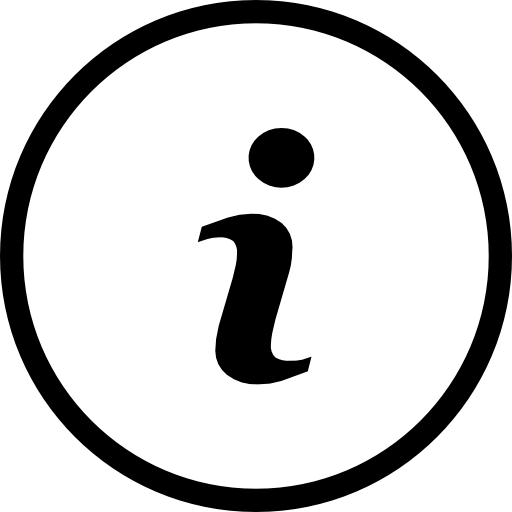
Now Howrah Bridge, the silent hero of many a film, including one by the same name, is completing 75 years. At a Victoria Memorial seminar, I had occasion to slip into a rare retrospective mood, telling the story of a bridge. How many Calcuttans remember this bridge was a replacement for one on floating pontoons, designed by Sir Bradford Lesley? It had a removable central section to allow river traffic that fed Calcutta port! Designed for a life of 25 years, it had to serve for 69 years, till the “New Howrah Bridge”, as it was called then, was inaugurated in 1943. The old one was struggling with the ever-growing traffic across the river to Howrah, which housed the main railway station and was the gateway to Calcutta. It also had to convey the raw material sourced from the rest of India for Britain via the port, and the finished materials from the colonial masters to the populace of the colony. It was the main artery of empire, and it was choking! The new bridge, therefore, was designed to have a road carriageway of 71 feet, enough to accommodate eight lanes of traffic, including two tram tracks, and, additionally, two 15-ft-wide footways on either side, keeping in view the huge pedestrian traffic disgorged by the railway station.
Interesting debates shaped the new bridge. Port authorities vetoed a foundation inside the river channel, fearing that would change siltation patterns permanently and affect ship movement. That dictated the broad plan—the bridge was forced to have a span of 1,500 ft. The designers decided on a balanced cantilever suspension bridge: a 1,500-ft-long ropeway of steel, slung on two towers rising about 300 ft above the ground on either side. A mammoth 26,500 tonnes of steel work! The 1,500 ft length has three parts. Two arms of 470 ft each cantilevered from the towers—at a gentle slope of 1 in 40, to make it easy for bullock carts and manual carts that made up the bulk of traffic—which in turn support a central suspended girder of 560 ft. The arms have two short anchor spans, held down by massive concrete anchor blocks behind each tower. If you stand bang in the centre, you may not realise you’re being held aloft in the air by anchors 1,000 ft away!
Stirrings against total domination by Britain too inflected this essay in steel. The UK-based Cleveland Bridge, the selected contractors, faced off against British-owned but Calcutta-based structural fabrication companies, which insisted the contract should not be awarded to any company from outside India! The claim of the lowest tenderer from Germany was brusquely dismissed because of the growing war clouds in Europe. Finally, a compromise was arrived at: Cleveland would get the construction contract, and the entire fabrication would be subcontracted to the ‘Indian’ players, who merged to form ‘The Braithwaite, Burn & Jessop Construction Co. (BBJ)’. The skills they picked up doing Howrah Bridge allowed them to do almost all major steel bridges across India and abroad for the next 60 years, including the next bridge across the Hooghly, the Vidyasagar Setu.
Then came steel—this needed ‘high tensile’ stuff, almost 1½ times stronger than what’s normally used, euphemistically called ‘mild steel’. It wasn’t manufactured in India those days—but the Tatas put their foot in the door and promised to upgrade! Finally, 23,500 tonnes of the total 26,500 was forged at Jamshedpur. The foundation work saw high-tech digging at levels much below the river bed. They were pioneers and martyrs diving into aqua incognito: Bend Disease, caused by the formation of nitrogen bubbles in the bloodstream, felled a few. When it was completed, on cue within five years, it was the middle of WWII. Howrah Bridge went under the cover of barrage balloons to evade Japanese bombs! It still eludes our attention, Calcutta’s proud and silent icon, uncorroded, a testimony to India’s skills.
(The author has engineered many bridges in India and abroad in a 60-year career.)